LAMINATE FLOORING
Laminate is a stylish flooring option that is made to endure.
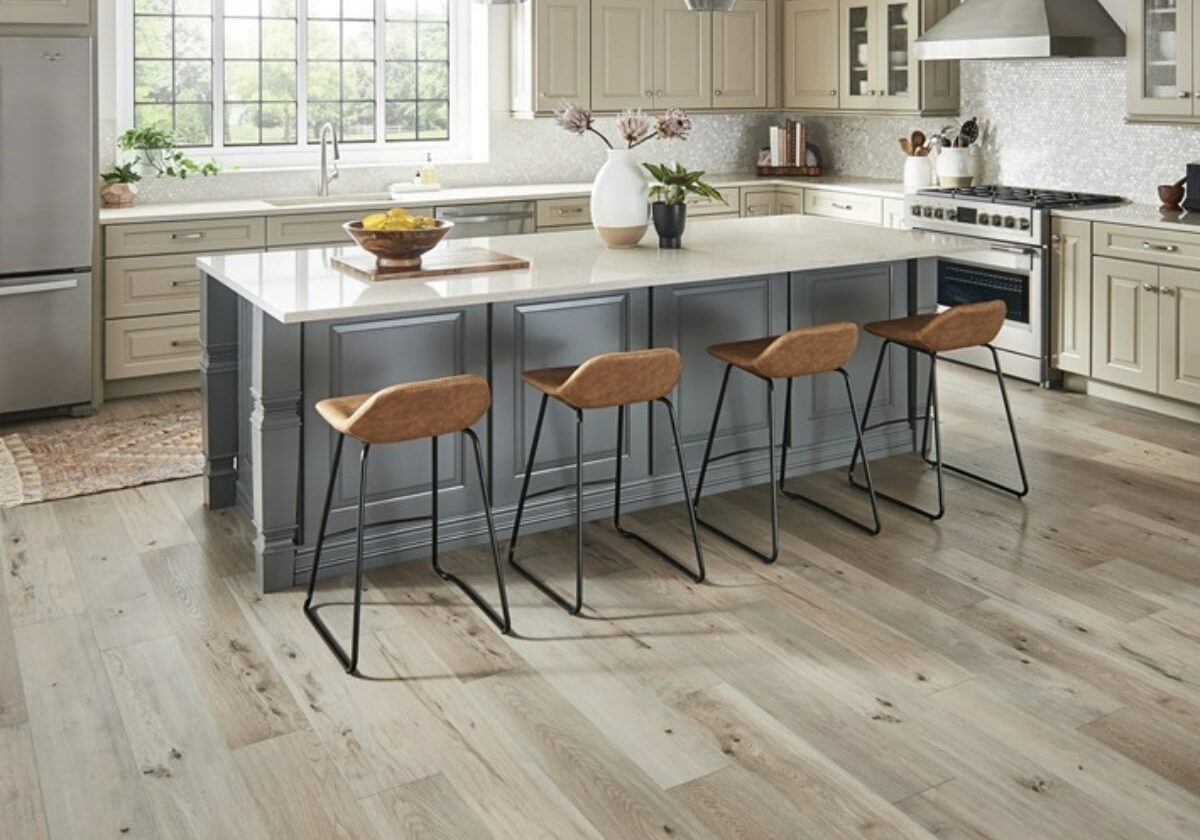
Quality Laminate Flooring For New Homes
Create a fashionable space with beautiful laminate flooring. Laminate is made to mimic the tones and characteristics of hardwood flooring, but is sought after because it is easier to care for than natural wood floors. Laminate will create a warm, inviting space, and is available in a wide selection of tones, colors, textures, and sizes to complement any home. Homeowners will love the strength of laminate, which is resistant to water, fading, scratching, and wear and tear.
At The L&L Company, we carry quality laminate flooring from today's top manufacturers so we can provide you with the latest trends and innovations for flooring homeowners will love for many years.
We are the preferred laminate flooring provider for builders in the Mid-Atlantic, and we look forward to working with you to create the perfect space.
Why Choose Laminate Flooring?
Not only is laminate an incredibly versatile flooring option, but it is also strong and made to stand up to even the busiest of households. Laminate is pet-friendly and kid-friendly, as well as made to stand up to high-traffic areas, making it a great option for families.
Laminate can be installed in most rooms of the home for a consistent design throughout, creating a beautiful home that families will fall in love with.
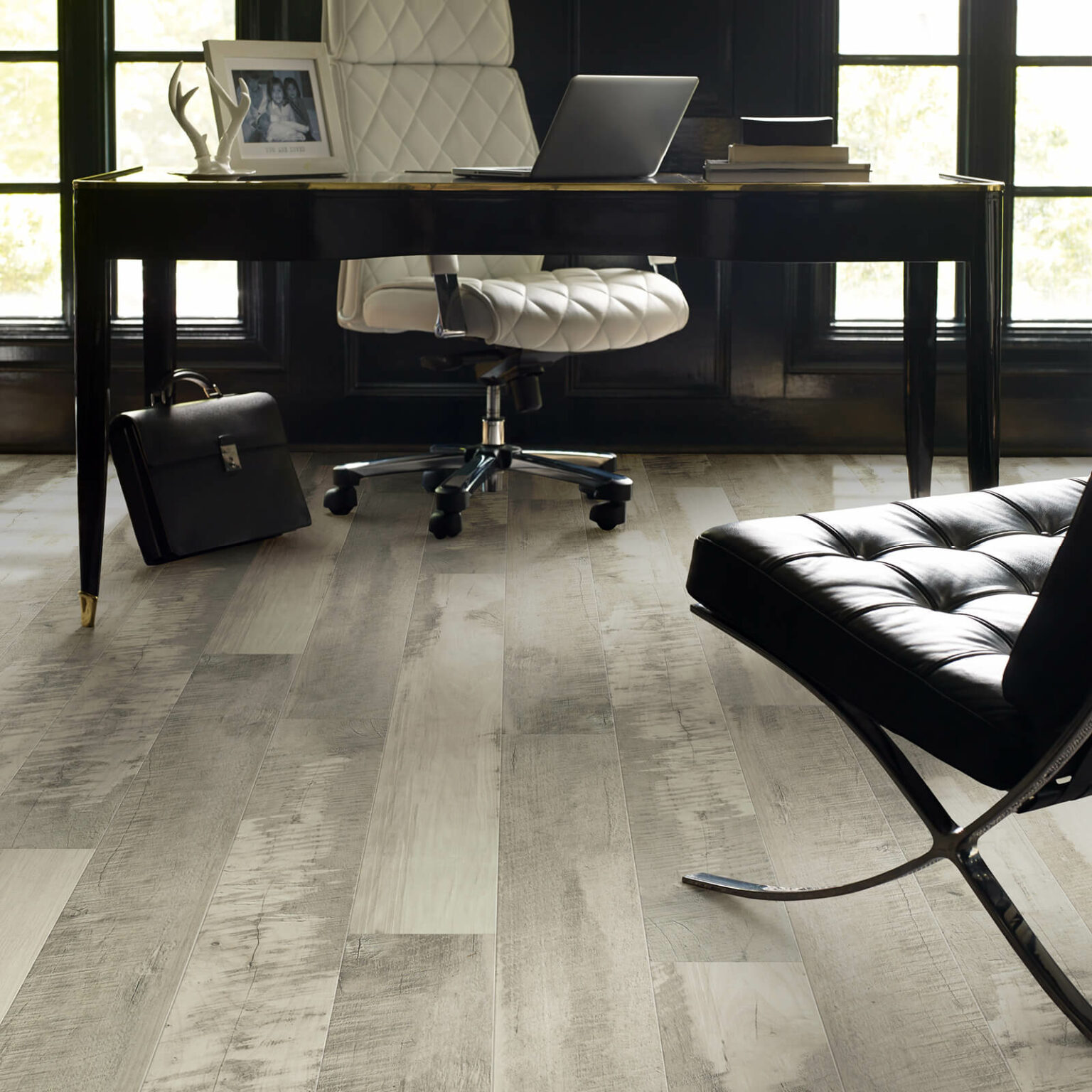
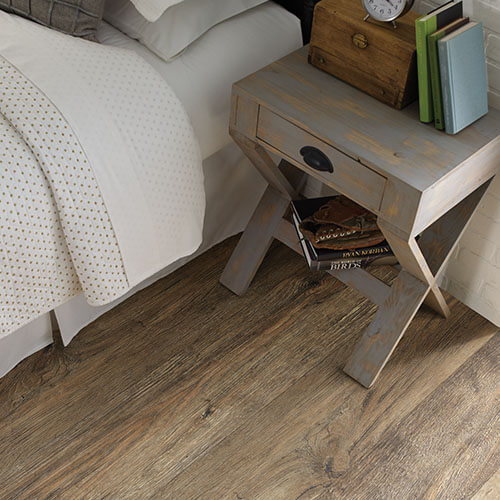
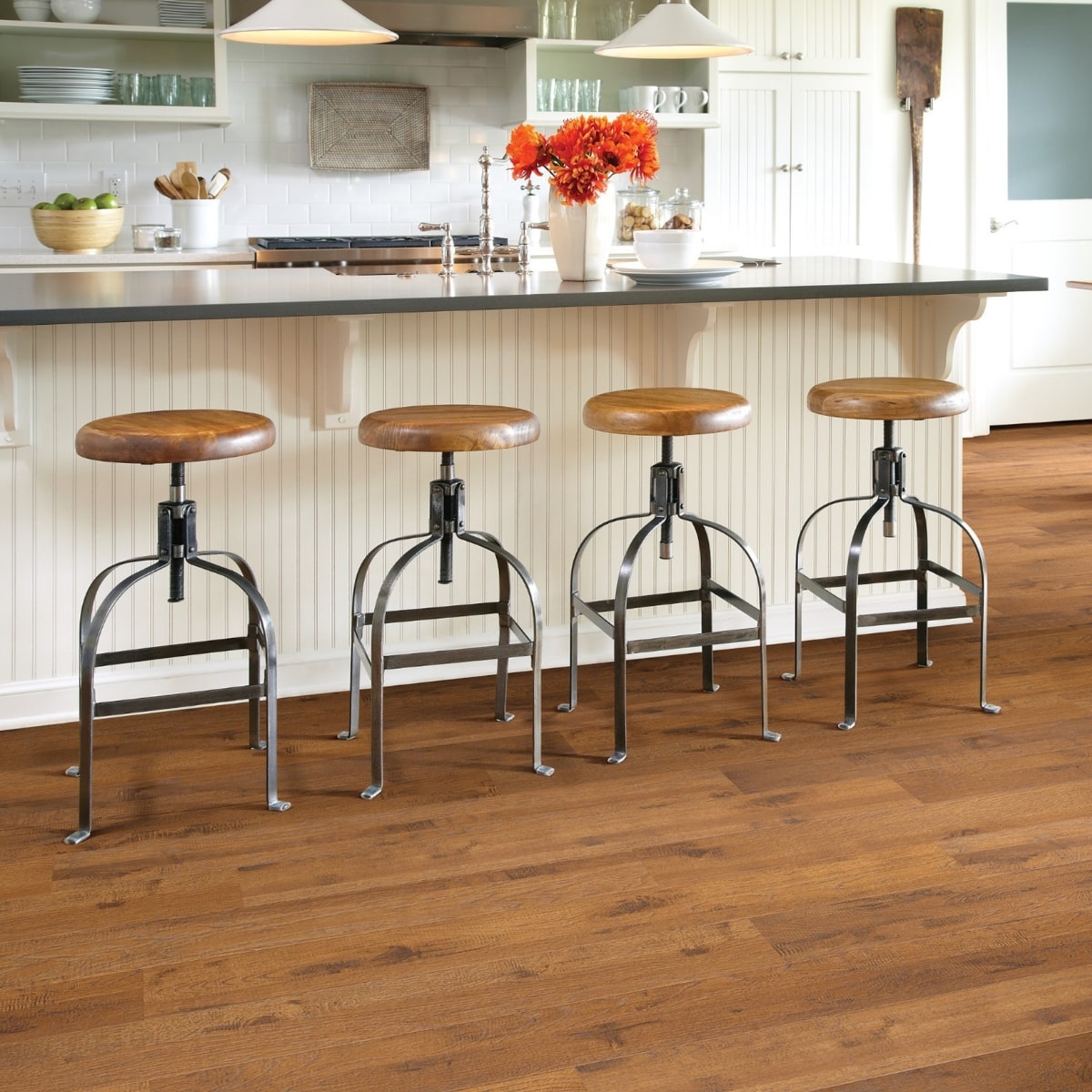
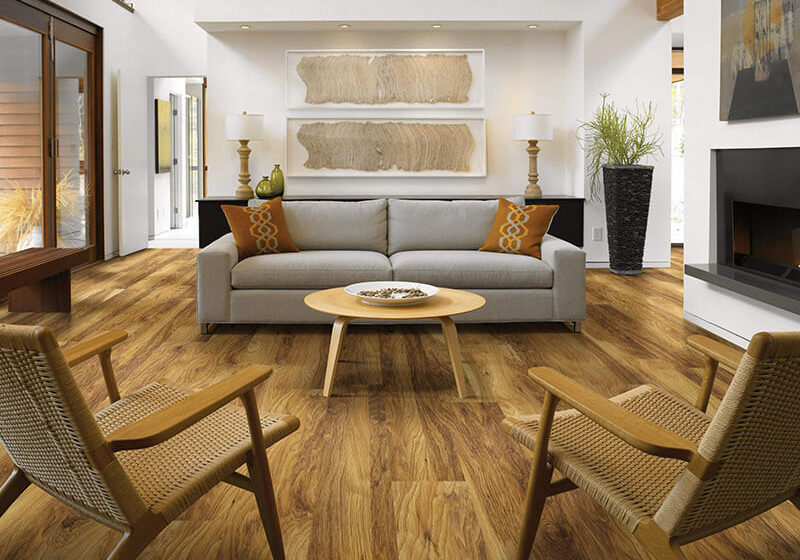
Need Inspiration?
Take a look at our laminate inspiration gallery! View the latest trends and ideas perfect for your homes.
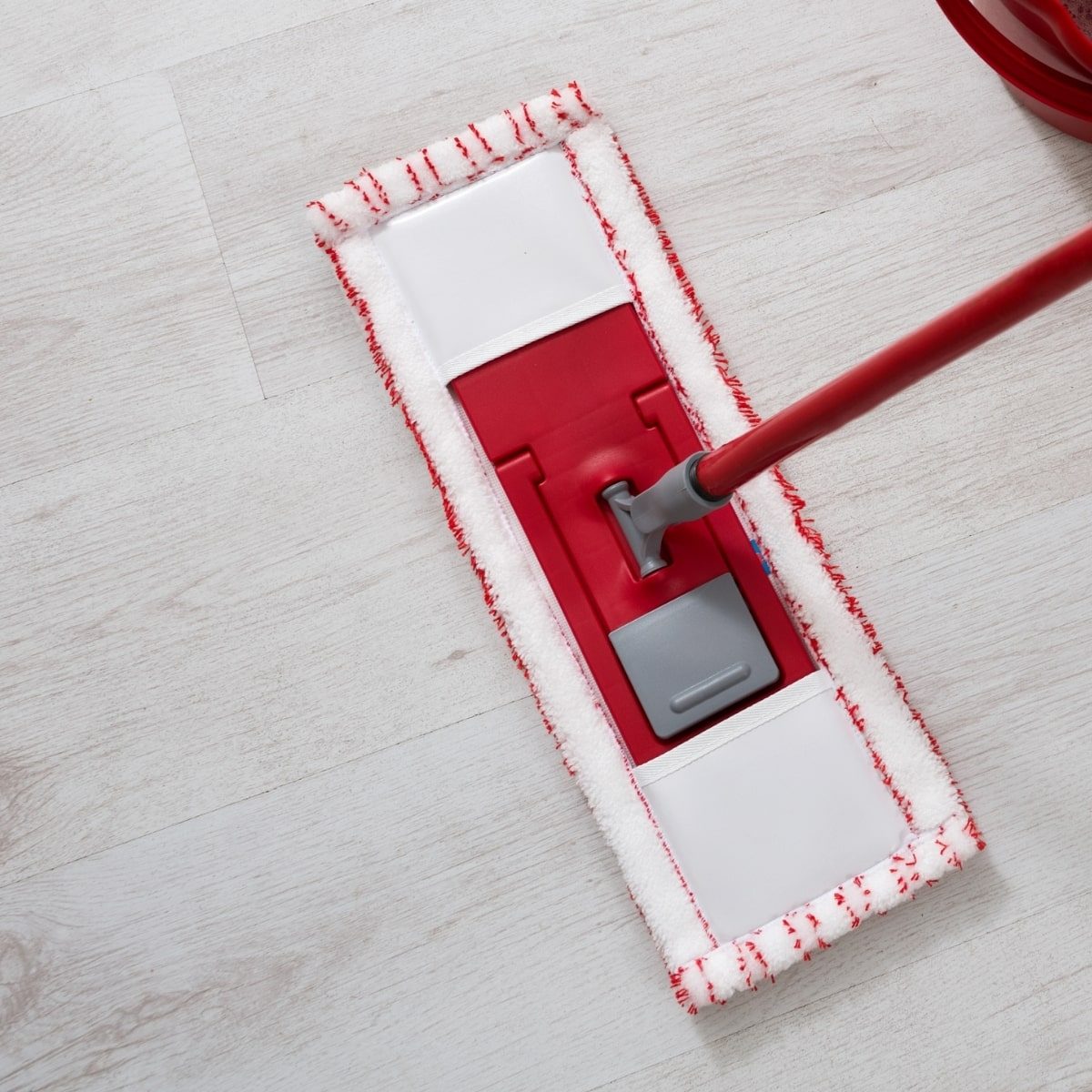
Laminate Care & Maintenance
Learn how to keep laminate flooring looking beautiful for many years.
Learn More About Laminate
Before you Buy
Before you buy laminate, own this knowledge.
Whatever your flooring budget, you need to be assured that once you make your purchase you know all the basic facts about your flooring choice.
Buying laminate flooring is no exception.
It pays, today and tomorrow, to know not only the basics but also some of the specifics.
That’s why we offer you this section.
It’s a summary of many of the things you should know about laminate before you buy.
That way your final decision not only creates a warm, inviting environment in your living spaces but also delivers what laminate floors are noted for: excellent durability and easy maintenance.
This flooring stands up and stands out.
Laminate flooring is a remarkably durable surface, stain resistant, and does not need to be varnished or waxed so it’s very easy to maintain.
These are floors for busy households, especially homes with kids and pets.
Today’s laminate styles consist of authentic wood visuals, rich ceramic looks or natural stone designs with different surface textures to beautifully accommodate any room in your home.
Understand this about pricing.
When considering laminates, you will notice that there is not much price variation in styles.
This is due to the relatively uniform manufacturing process for all laminates: no matter what the style, color or type, it is still a photograph that provides the decorative surface.
The more expensive laminates include those with a textured and more natural looking surface with a greater number of screens.
Laminate floors that simulate the more exotic varieties of hardwood flooring quickly rise in price. So keep that in mind.
However, higher-end laminates are more durable and have extended warranties.
What you should know about “floating”.
Laminate floors are installed using a “floating floor system” in which a padded underlayment sits between the subfloor and the laminate planks.
The planks sit directly on the underlayment and are not anchored to the subfloor on the bottom but rather anchored by the edges.
When walked upon this type of installation can produce a hollow sound and have a slight give.
Slight ridging or peaking where planks are joined together may also occur. This is considered normal and nothing for you to be concerned about.
Some laminate floors lock together without the use of adhesive on the sides of the planks. These are glueless installations.
Glueless laminate floors have planks that simply interlock together. These floors make for easy repair if that is ever necessary for you down the road.
Get on top of the bottom line. Know the entire cost of ownership.
The “cost per square foot” of your laminate floor is just one component of the entire project cost. To ensure there are no surprises, and the laminate you select fits within your overall project budget, be sure to ask us to calculate the total cost of your floor covering project.
Here’s a list of potential additional expenses you may incur:
- Furniture removal/replacement.
- Demolition/disposal of old floor covering. Depending on the existing floor covering, this can be an expensive item; also, be sure to include the cost to dispose of the old floor covering.
- Subfloor preparation. Depending on the condition of the subfloor, it may require additional work.
- Product delivery.
- Laminate installation. Determine the cost per square foot to install it.
- Materials required to complete the installation. Your new laminate floor may require additional materials to install it properly.
Be sure to also consult the manufacturer’s warranty and care guide for directions on how frequently the floor should be cleaned and the cost to clean it.
There’s a lot to know and keep in mind before buying a laminate floor, but it’s well worth the effort. If you’re a smart and knowledgeable shopper it will show where it counts – in a beautiful, durable and easy to care for floor.
How it's Made
All you need to know about laminate construction.
Learning how laminate is manufactured is easy and simple. We’ve outlined
the basics below and ask that you read through them to better understand how this
unique product is created.
Knowing how laminate is constructed provides you with knowledge of laminate right from its beginning. That’s important information because these are the
materials you’ll be living with and walking on for years to come should you choose
this flooring product.
Knowing laminate construction also helps you better understand and evaluate its performance aspects.
So read on, and we’ll do our best to help you know how laminate is made,
the various steps involved, and the reasons why certain processes are performed.
In the section “Introduction to Laminate,” we told you laminate is a manufactured product that is a true look-a-like of hardwood flooring, natural
stone and many other types of flooring.
Now, you may be wondering, how can laminate flooring resemble these other
products so closely?
The answer lies in the process of how laminate is made.
It’s a combination of the precision of today’s manufacturing
techniques and the expertise of the men and women behind the materials, machines and methods that create laminate.
All work in harmony to produce a beautiful, functional flooring that closely
simulates other beautiful, functional floorings.
To know laminate, think baking and a four-layer cake.
Today’s laminate floors are available in a multitude of designs, patterns, and textures, yet they all consist of four main components that are bonded
together.
The bottom layer, or backing, is a melamine plastic layer that lends dimensional stability to the planks and also helps guard against moisture from the sub-floor. (Moisture infiltrating any flooring is the enemy.)
The next layer is a core board, generally made from high-density fiberboard or
particle board which may also contain melamine plastic resins that help improve the
moisture resistance of the core.
Then a decorative layer or print film is adhered on top of the core board giving the floor its hardwood or tile look.
This decorative layer is a printed high-resolution photo-reproduction of wood
grain, natural stone or ceramic tile pattern. (Now you know how the look-a-like is
born.)
And the frosting? On the top of our “cake” is a durable wear layer, providing protection and stain resistance.
Now many wear layers also contain aluminum oxide, as well as melamine resin, and that creates exceptional durability. The kind that will stand up to the most
active household – even yours.
All four layers of our “cake” are then combined in a high-pressure
process.
Now we’ll take you through the manufacturing process of laminate one step at a time.
Step 1: stacking with electronic precision.
The process begins with the assembly of the 4 layers of raw materials in large
sheets.
This typically takes place on a production line, where modern technology enables each layer to be stacked on top of another with incredible accuracy and
precision.
How precise you may ask? Most manufacturers use sophisticated electronic
calibrating equipment and digital camera systems to keep the sheets in perfect alignment.
The backing layer is first on the line, with the core board placed directly on
top of that.
Next, the printed decorative layer is stacked on top of the core board. The final layer to be stacked on is the wear layer.
Step 2: now the pressure is on.
Once the 4 layers have been stacked, they are ready for pressing.
The presses used to create laminate flooring have hydraulic rams that apply
tremendous pressure to the stacks.
The stacks of layers are pressed at high temperatures reaching 400 degrees
Fahrenheit, with up to 600 pounds per square inch of pressure for 20 to 30 seconds.
Manufacturers carefully monitor the time and temperature when pressing the layers to successfully cure and bond the stacks into a single sheet of finished
decorative laminate.
If the laminate that is being manufactured is designed to have a textured
surface, the press has specialized plates that imprint the textured pattern onto the
sheets, creating more natural looking planks or tiles.
Step 3: a time out to cool off.
After the sheets are pressed they are left to cool to ensure that they fully cure and to prevent any surface imperfections.
Then the sheets are stacked and stored for a time so that they can continue to
acclimate, thereby enhancing the stability of the boards.
Step 4: planks, profiling and precision.
Once the boards are fully acclimated, they are milled, or cut into planks.
The freshly cut planks then move on to be profiled. Multiple profiling saws
create the tongue and groove edges on the sides of the planks that enable the floor to lock together with ease.
The blades on the profiling saws use electronic and laser systems that produce
incredibly accurate edges for a perfect fit. Further assurance of the precision of your
floor.
The finished planks then go through a quality inspection and are checked for
color, texture, finish, size and correct interlocking capabilities.
Once approved, the planks are then stacked, packaged and loaded onto trucks for distribution.
Now that you know how laminate flooring is made you can understand why it’s a beautiful, durable and cost-efficient flooring answer for many homes, and homeowners, across the county.
laminate Styles
Knowledge about laminate styles.
Laminate offers you a large family of styles and our goal is to help you understand the big picture on installation types when it comes to this unique family of flooring products. This information will let you shop smarter and compare with confidence.
For many of us, when it comes to picking a style of any product, we usually “know it when we see it.” Perhaps that describes you, too.
Well, if laminate interests you, it’s virtually guaranteed you’ll find a style that’s right for your home.
This section explainslaminate types of installation, and offers you all the information you need to make smart choices.
Is it real or laminate?
If laminates looked fake the last time you checked, it’s time to check again !
Today’s laminates are looking better and better, and often need close examination to be identified.
Laminates have truly come a long way. Why?
Because of the growing popularity of laminates, manufacturers are creating an increasing array of traditional, rustic, and exotic wood grain designs.
In fact, presses have improved to the point where the texture imprinted on top of the design looks more real than ever, even with distressed wood or natural stone designs.
Want to know what’s new under the laminate sun?
As with sheet vinyl floors, some of the new laminates really have the look of natural materials, particularly the textured products that give the floor dimension. The most common, basic laminate designs have a wood grain appearance.
Some of the most popular laminates have rustic or historic wood grain patterns.
If you’re curious about what are the best sellers, it’s the natural stone look-a-likes, particularly slate and tumbled tile varieties.
Quality is focused on the photography.
The quality of the laminate partially has to do with the photography and the number of photographs per style, which is known as "screens" .
Here’s an example for you. When manufacturers emulate a natural stone tile, they try to recreate the variation in color, pattern and texture that is a result of cutting a natural product.
The more screens a product has, the more variation it can offer. And the more “authentic” the laminate looks.
Understand this about color.
Like any floor, select the laminate color to compliment the size of your room and the activities taking place in it.
Remember that lighter colors will make a smaller room appear larger, while darker colors will absorb the light and create a more intimate setting.
Choose a color that either coordinates or contrasts with your cabinets and other furniture. Avoid matching everything to the same color and style.
Let your creativity guide you ! And remember, contrasts can make your room more interesting.
Laminate flooring types – yours will be installed in one of these 4 forms. Glueless laminate flooring.
No mess, glueless installation makes these floors quick and easy-to-install.
They come in a variety of ceramic and wood designs and colorations, as well as some manufacturers offer a real, hardwood veneer instead of a printed layer. It looks amazingly hardwood-like.
These floors come in both planks and squares. A thin, plastic underlayment is needed to seal out moisture from below. (Remember, moisture is the enemy of your flooring.)
In fact, most laminate floors require a plastic underlay sheet (4 mil poly) be installed directly underneath the laminate planks or tiles.
This helps the floor float freely over the subfloor. Another option is to add a vapor barrier or noise reduction underlay before installing the laminate flooring.
Laminate flooring with attached underlay.
These floors come with several different types of tongue and grooved locking systems and an attached underlayment to reduce noise levels. That’s good to know.
Glued laminate flooring.
These are the original laminate floors that do require a special formulated glue to be applied to the tongue and grooved areas for each plank.
Once the glue is dried the planks are almost impossible to pull apart. These floors are offered in both planks and squares.
Pre-glued laminate flooring.No mess, because the glue is already applied to the tongue and grooves which makes these floors quick and easy-to-install.
A thin, plastic underlayment is needed to seal out moisture and prevent the glue from sticking to the substrate.
Moldings are the finishing touch.
Laminate moldings also affect the overall style and give your room a beautiful finished look.
Moldings are important because they cover the space that is allowed for the flooring to expand and move naturally on top of the subfloor, and they help with the transition to an adjacent floor.
Most manufacturers offer coordinating moldings for all styles and colors for any laminate flooring you choose.
However, be aware that moldings for laminates are slightly larger than their wood or ceramic tile counterparts.
Here, to familiarize you with various standard moldings, are some styles and definitions.
The Step Down Stairnoseis a coordinating piece providing the proper transition for all the steps in your home.
A Reducer Stripis the transitional piece the installers use to connect the laminate with another type of floor covering such as vinyl, thin ceramic tile, or low-pile carpeting.
An End Moldingor Carpet Reduceris used as a transition from laminate floors to different flooring surfaces when the reducer does not allow enough height, such as on high-pile carpet or thick ceramic tile.
T-Moldingis commonly used in doorways to join two laminate floors in adjoining rooms. It's also recommended when making transitions from a laminate floor to another floor that is approximately the same height.
Finally, a Quarter Roundmay be installed wherever the laminate floor meets the wall or baseboard.
We recommend that you work closely with us to become familiar with the moldings and transition pieces.
Ask to see samples if possible, so there are no surprises come installation time.
With a lot of knowledge, hopefully from the above, and a little imagination (that’s your department), you will find a laminate flooring that is just right for you and your home.
laminate Glossary
For definitions of other terms not listed here, please go to these sections: How It’s Made, Styles, Before You Buy and Installation.
Acclimation The adaptation of the laminate floor to its installation environment.
Backing In laminate flooring, the bottom layer, or backing, is a melamine plastic layer that lends dimensional stability to the planks and also helps guard against moisture from the sub-floor.
Decorative Layer In laminate flooring, a decorative layer or print film is adhered on top of the core board giving the floor its hardwood or tile look. This decorative layer is a printed, high-resolution photo-reproduction of wood grain, natural stone or ceramic tile pattern.
End Molding/Carpet Reducer Used as a transition from laminate floors to different flooring surfaces when the reducer does not allow enough height, such as on high-pile carpet or thick ceramic tile.
Floating Floor System Laminate floors are installed using a “floating floor system” in which a padded underlayment sits between the subfloor and the laminate planks. The planks sit directly on the underlayment and are not anchored to the sublfoor on the bottom but rather are anchored on the edges.
Glued Laminate Flooring These are the original laminate floors that do require a special formulated glue to be applied to the tongue and grooved areas for each plank. Once the glue is dried the planks are almost impossible to pull apart. These floors are offered in both planks and squares.
Glueless Laminate Flooring A no mess installation method where the planks or squares simply interlock together.
Laminate Is a manufactured product that simulates the look of hardwood, ceramic tile, natural stone and many other types of flooring.
Melamine Resin Used to help improve the moisture resistance and durability of the core board of laminate flooring.
Moldings Trim pieces that cover the space that is allowed for the flooring to expand and move naturally on top of the subfloor. They also help with the transition to an adjacent floor. Moldings for laminate floors are slightly larger than their wood or ceramic tile counterparts.
Overlapping Stair Nosing Similar to a flush stair nosing except the nosing overlaps the exposed edge of your floor. The overlapping stair nosing is secured to the sub floor and not to the laminate floor so the floor is free to move
Peaking Seams that have raised where the laminate planks or tiles join.
Plank A laminate floor panel that is typically 5 or 6 inches longer than wide.
Pre-Glued Laminate Flooring A no mess method of installation because the glue is already applied to the tongue and grooves. A thin, plastic underlayment is needed to seal out moisture and prevent the glue from sticking to the substrate.
Quarter Round Trim Installed wherever the laminate floor meets the wall or baseboard.
Reducer Strip The transitional piece installers use to connect the laminate with another type of floor covering such as vinyl, thin ceramic tile, or low-pile carpeting.
Screens The quality of the laminate partially has to do with the photography and the number of photographs per style, which is known as "screens". The more screens a product has, the more variation it can offer. And the more “authentic” the laminate looks.
Seams The junction where the panels connect together.
Square Nosing / Universal Edge Used where the laminate flooring butts up to carpeting, or various vertical surfaces where the edge will be exposed, such as along a fireplace.
Step Down Stair Nose A coordinating molding piece providing the proper transition for all the steps in a home.
Tile A laminate panel in a geometric shape – square.
T-Molding Commonly used in doorways to join two laminate floors in adjoining rooms. It's also recommended when making transitions from a laminate floor to another floor that is approximately the same height.
Underlayment A material used between the laminate flooring and the subfloor that acts as a sound and moisture barrier and also allows the floor to expand and contract with changes in the temperature.
Wear Layer The durable, top layer of laminate flooring. It provides protection and stain resistance. Many wear layers also contain aluminum oxide, as well as melamine resin, and that creates exceptional durability.